In the realm of restoration builds, maintaining impeccable quality control is paramount. It's not merely about completing a project; it's about ensuring that every aspect of the restoration meets the highest standards of excellence. Sabra Johnson, a seasoned professional in the industry, emphasizes the significance of having a robust system in place and adhering to a meticulous checklist. In this insightful guide, we delve into Sabra Johnson's proven method for achieving unparalleled quality control in restoration projects.
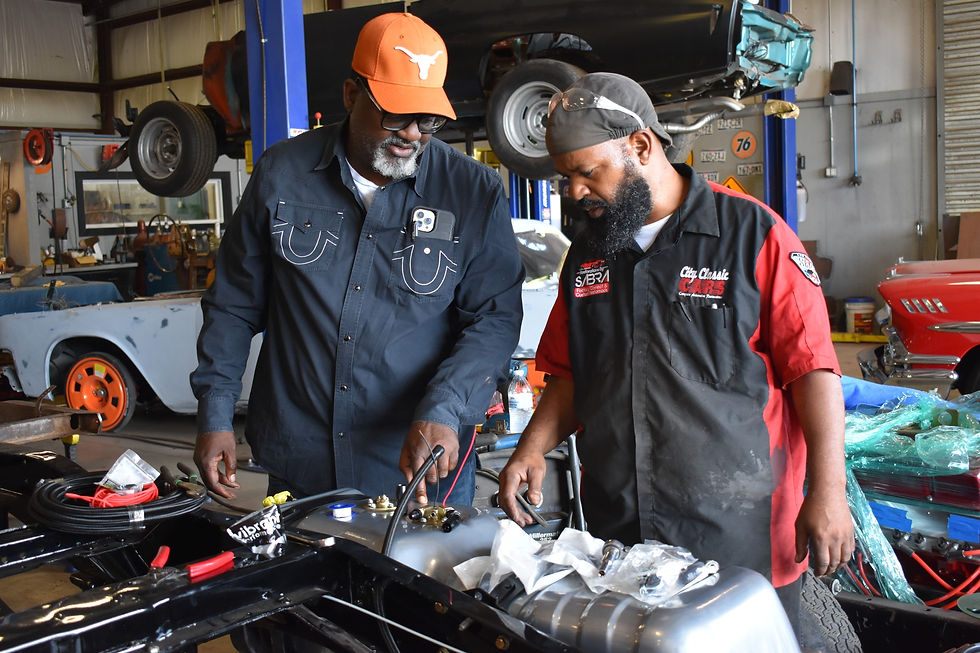
Understanding the Significance of Quality Control
Before diving into the specifics, it's crucial to grasp why quality control holds such immense importance in restoration builds. At its core, quality control is about consistency, reliability, and ultimately, client satisfaction. By upholding stringent quality standards, builders not only bolster their reputation but also instill confidence in their clients, leading to repeat business and positive referrals.
Establishing a Systematic Approach
Sabra Johnson emphasizes the need for a systematic approach to quality control. This begins with the development of a comprehensive plan that outlines every stage of the restoration process. From initial assessments to final inspections, each step must be meticulously documented and adhered to. By creating a structured framework, builders can minimize errors, enhance efficiency, and deliver consistent results.
Crafting a Detailed Checklist
Central to Sabra Johnson's method is the use of a detailed checklist. This document serves as a roadmap, guiding builders through each phase of the restoration. It should encompass all essential tasks, including material sourcing, construction procedures, and quality assessments. Regular updates and revisions to the checklist ensure that it remains relevant and reflective of evolving standards and best practices.
Implementing Quality Assurance Measures
Quality assurance is integral to maintaining high standards throughout the restoration process. Sabra Johnson emphasizes the importance of proactive measures, such as conducting regular site inspections, monitoring progress, and addressing any issues promptly. Additionally, fostering open communication channels ensures that concerns are promptly addressed, mitigating potential setbacks and ensuring timely project completion.
Leveraging Technology for Efficiency
In today's digital age, technology plays a pivotal role in enhancing efficiency and accuracy in restoration builds. Sabra Johnson advocates for the integration of innovative tools and software solutions to streamline processes and facilitate seamless communication. From project management platforms to mobile applications for onsite assessments, leveraging technology empowers builders to optimize their operations and deliver superior results.
Prioritizing Training and Development
Investing in the ongoing training and development of staff is another cornerstone of Sabra Johnson's approach to quality control. By providing team members with the necessary skills and knowledge, builders empower them to uphold the highest standards of craftsmanship and professionalism. Whether through workshops, certifications, or mentorship programs, ongoing education fosters a culture of continuous improvement and excellence.
In conclusion, Sabra Johnson's builder-to-builder tips offer invaluable insights into enhancing in-house quality control in restoration builds. By implementing a systematic approach, crafting detailed checklists, and leveraging technology, builders can ensure consistency, reliability, and client satisfaction at every stage of the project. Through a commitment to excellence and continuous improvement, builders can establish themselves as industry leaders, delivering unparalleled quality in every restoration endeavor.
Restorations By Sabra
16548 Stuebner Airline Road
Spring, Texas 77379
832-717-0774
Comments